The big shock
Ann and
I returned to Port Napoleon in February 2005 after leaving Ruffles Spray there
to visit Ann's daughters and to spend Xmas with them. The plan was to remove
all of the loose paint on the topsides then repaint. Under water we were going
to sand back and put on two new coats of epoxy primer then re anti foul.
I carefully examined the under water area and found small areas that looked
like leopard spots. This was serious I thought and decided the best course of
action was to re shot blast the under water area and start from fresh. I went
to Yachting Services in Port Napoleon and asked for a quote for them to shot
blast 55 square meters of steel. Their reply was Euro 7500.00. I nearly had a
heart attack. I could have the whole boat shot blasted for that money and
walked out in discussed.
There was another company that specialised in painting of yachts, D & S
Marine, Stephen Berry was the owner and was British. He looked at the areas in
question and said he thought that it was electrolysis. Not a word I wanted to
hear. He said he would get his expert to have a look the next day. The next day
came and Stephen reported back. Not electrolysis but entrapments of paint
solvents within the epoxy. The problem did not go through to the steel and the
expert thought that the first primer coat was sound. This problem usually came
from old paint and sometimes from coats being applied to fast and to thick.
So what to do. I still thought that shot blasting to bare metal was the answer
and Stephen took another look at the job. He suggested that he blasted from
where the side walks joined the coach roof sides to port, down the topsides and
all the way to the coach roof side to starboard. OK, good plan and probably the
best solution but how much will this cost? £ 3500.00 for blasting back to bare
metal four coats of high build epoxy primer, and three coats of two pack top
coat and a coat of anti fouling. Wow, what a great deal. Just over Euro 5000.00
and the whole yacht would be back to normal. We had a think about it. Ann and I
went over to Ruffles Spray and started to think about what else we could change
whilst we had a chance. Ann said she wanted stainless steel railings all round.
OK I thought I can cut of the old and weld on new. She also said that we could
weld on a gantry to take solar panels, wind generator and all of the gadgets I
needed. I though it would be a good idea to extend the dog house roof all the
way over the cockpit. The reason for this was that we currently had a canvas
enclosure that we had made ourselves. This was always up. In the summer to keep
the sun off and in the winter we would add side and rear panels to give us a
fully enclosed cockpit. Ann suggested that we fit two hatches into the roof
facing forwards, which would give us good ventilation and allow cool air into
the cockpit. We were going to make two of the dog house windows opening but
this was a better idea as it would leave the integrity of the doghouse intact.
Ann wanted a bathing platform and I agreed it would make life much easier.
So, back to Stephen and another question. How much to shot blast those
additional areas like the roof extension etc. He said it would be easier to do
the complete boat. He punched some numbers and gave us a revised cost. Euro
8500.00 for the entire job which consisted of:
a. Shot blast complete vessel to SA 2.5
b. Four coats of epoxy high build primer at least 300 microns per coat.
c. Three coats of two pack gloss colour of our choice
d. Two coats of anti foul
e. Guaranteed for three years
Well I was very pleased. However, even though we had a good income from our
business back in the UK
we did not have a spare £6000.00 hanging around. OK we thought we would go back
to the UK
and work a little more on our business. So we accepted the quote.

Work starts
Now the
serious planning started. I had to do all of the steel jobs before Stephen
could start. I estimated that I would need until the summer to do them. We told
Stephen to send us the costs in writing and that we would return to the UK to cost our
side of the project. So back we went to Bristol.
It took two weeks to cost it all and the material list was as follows:
a. 85 meters of 25mm diameter stainless steel tube highly polished
b. One sheet 2400mm x 1200mm x 4mm pre shot blasted and primed steel plate
c. 30 meters of 50mm diameter stainless steel tube highly polished
d. 10 meters of 50mm x 4mm stainless steel flat bar
Cost for all this was just under £2000.00. Cheap at the price. We booked our
ferry for the end of March to start the job.
Back in Port Napoleon I cut off all of the old railings, doghouse frames and
davits. To cut a long story short it took a whole month to complete the work.
It was now the beginning of May and we returned to Bristol to continue to work our business.
Stephen had told us he could not start until July anyway which was a good thing
as we needed the time to get the money together to pay him.
Meanwhile I was also checking into the various components we wanted to add to
Spray to make our life more easy. The list was:
a. Four 90 watt BP solar panels
b. One regulator for the panels
c. Forward Looking Sonar by Echopilot
d. Shenker water maker 35 litres per hour
e. Two new through hull fittings complete with seacock (one for watermaker and
one for galley sink drain)
f. Bow thruster complete with tunnel
g. 60 feet of 4” x 1” teak planks for the bathing platform
h. Four Vetus dorade vents
i. Six 225 AH 6 volt Trojan deep cycle batteries
j. Cabling upgrade for batteries and other equipment
k. 1500 watt inverter
l. More sound proofing for the engine room
m. Engine room ventilation upgrade
n. New cockpit seat foam and covers
o. Electric winch
p. Clipper Wind speed and direction indicator
q. New shower tray and fittings
r. 2 x 2 way valves for toilette direct to sea
s. Wood for Instrument Panel for doghouse and nav station
t. New windows for dog house
u. Change from cleats to 2 x double 4 x single spinlock mini jammers
v. Various extension cables
All this came to £12,000.00 or so. We returned to Port Napoleon at the
beginning of July. We had agreed with Stephen that the boat would be ready for
blasting on the 15 August 2005. A lot of work was yet to be completed. I had
the mammoth task of welding in the bow thruster tunnel. First the whole of the
heads compartment needed to be removed. This took ages, as I did not want to
damage the walls or any of the lockers. This done I started to mark up where I
was going to cut. A French chap in his 6o’s started to give me some
advice on how to cut tunnel area. He did not speak English and I could only
order a beer in French so it was tricky. Anyway as far as I can gather he was
going to come back the next day and check up on me. So be it I thought better
get on with it after wasting an hour talking he in French and me in English.
It took three complete days of work to finish the tunnel. My days consist of 12
hours when I am working on the boat so it took a long time to finish. Next came
the galley sink drain and the intake for the watermaker. This completed the
next job was the Forward Looking Sonar (FLS) through hull. Prior to leaving for
France I asked Echopilot about the through hull fitting and they advised that
they can supply a steel through hull fitting which is just like a plastic one
but made of steel. They wanted £250.00 for it to be made. I thought this was a
little steep and asked them if I could have a drawing so I could make my own.
Of course I could they said and faxed me a copy. The drawing was changed. The
whole fitting was re designed without a screw thread, the wall thickness was
increased so that it could be welded directly to the hull. I went over to a
local machine shop and asked if they could make it. They said no problem the
cost would be £75.00. A bit cheaper than the Echopilot one and it made more
sense to weld it in.
This new fitting was welded in. Next I made a new windlass mount so the chain
would be more horizontal in its run to the bow rollers. All of the steel work
was now complete and I asked Stephen how he wanted the boat masked up. He said
I needed to remove the windows and all of the deck gear. This took a whole
week. Next came the masking up. I had bought 500 meters of duck tape for the
job. It took three complete days to mask up all of the stainless steel work.
The worst job I had ever done. It was the evening of the 14 August and we were
ready. Ruffles Spray was ready to be shot blasted for the second time.
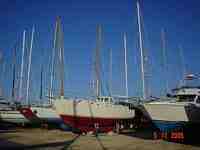
A new look Ruffles Spray
Stephen however was not ready. He was
still working on a large yacht, which belonged to a chap who owned a well known
ladies facial product company. Can’t give any names here but Stephen was
under a lot of pressure to finish this and he was behind schedule. So we
waited, and waited, and waited. We went down the beach and had a few days off.
Finally on the 29 August Stephen was ready. The boat was moved to the shot
blast area and shotblasting began. The next day the heavens opened and blasting
had to stop. The boat was covered in plastic sheet but the damage had been
done. The next day the whole job had to be started from scratch. It took until
9pm to finish. However, this was not the end as a primer coat had to be applied
that evening if the blasting was not to be repeated again. Stephen worked until
11pm that night and finished the first primer coat on the complete boat. His
airless spray system was fantastic. I’ve never seen anything like it.
The next day Stephen confessed that it would take three weeks to finish the
painting. We were not bothered now as we both were very tired. What was Stephen
suggesting that we do? He said it was now the 3 September, why don’t we
go back to the UK
and come back in October. The boat would then be completely cured and dry and
we could refit all of the bits. OK. This is what we would do. Back we went to Bristol and continued to
work our business.
We had a phone call in early October. Stephen wanted us to delay yet again. We
said we would come back on the 3 November and that all had to be finished by
then. He agreed. Port Napoleon has some fantastic things to offer people who
are refitting their boat. One of them is their inside storage facility. They
have a massive hanger the size of two football fields. In this hanger all work
can be completed in the dry and out of the wind. And does it blow there. It is
after all in the Golf de Lion. Renowned for its Mistral. In February the wind
was so strong it blew be off a plank of wood which was laid over two 50 gallon
drums. Very strong indeed. Now the boat had been inside since the beginning of
September and it was not very cheap to be there. This extra cost must not be
charged to me I told Stephen and he agreed.
Ann and I arrived back in Port Napoleon late on the 5 November 2005. It was
dark but I could not help but sneak a look in the hanger which had no lights.
Ann and I walked passed Ruffles Spray twice. We did not recognise her. Stephen
had done a fantastic job. It was worth the wait. We went to bed and got up
early to start the long list of jobs before Spray could see daylight again.
One of these jobs was to remove the duck tape from the stainless steel. What a
complete nightmare. It took Ann and I two days to remove it. Next we refitted
all the deck fittings, windows, windlass, doghouse windows and hatches. At last
Spray could be moved outside and the mast could be stepped. This done the yacht
was moved to the storage area on the hard. The container we had been renting
was moved in front of the boat and Ann and I loaded all of the gear back
onboard. Last we refitted the sails. Ruffles Spray looked like a yacht again.
We still had to fit the bow thruster but we could not do this until the spring.